Automatic Eye Drop Bottle Cartoning Machine
Model: CSZ-100B
Automatic Eye Drop Bottle Cartoning Machine equipped with a bottle sorting machine, automatically feed the bottles on to cartoning machine conveyor, and then fill it the box and sealing.
- Speed:30-90cartons/min
- Application Box Size:L(70-220)mm×W(14-90)mm×H(14-65)mm
- Cardboard Material:300-450g/㎡
- Power Supply:1.5KW 220V 50Hz
- Technical Parameter
- Electrical Parameter
- Application Samples
Model | CSZ-100B |
Packing speed | 30-90cartons/min |
Size of package | L(70-220)mm×W(14-90)mm×H(14-65)mm |
Cardboard material | 250-350g/㎡ |
Instruction material | 60-70g/㎡ |
Instruction size (Unfold) | (80-150) x (90-170)mm |
Instruction size (Fold) | (1-4) Fold |
Motor power | 1.5kw |
Power supply | 220V 50HZ |
Minimum Air pressure | 0.6Mpa |
Air consumption | 120-160L/min |
Maximum noise | 80dB |
Overall dimension | L3100mm×W1100mm×H1900mm |
Weight | 1500Kg |
PLC | CPIE-N30DT-D/Omron |
PLC Extened Module | CPIE-C1F11/Omron |
Touch Screen | NB7W-TW00B/Omron |
Sensor | E3Z-D61/Sick |
Frequency | 3G3JZ-A4015/Omron |
Relay | MY2 NJ24V/Omron |
Button | XB2/Schneider |
Emergency Stop | ZB2 BC4D/Schneider |
Electromagnetic Valve | 4V210-08/Airtac |
Pressure Regulator Valve | BFR-2000/Airtac |
Proximity Switch | TL-Q5MC1/Omron |
AC contactor | LC1E3210M5N/Schneider |
Air switch | 3P32A 1P6A/Schneider |
Vaccum Sounder | ABM20-C/SMC |
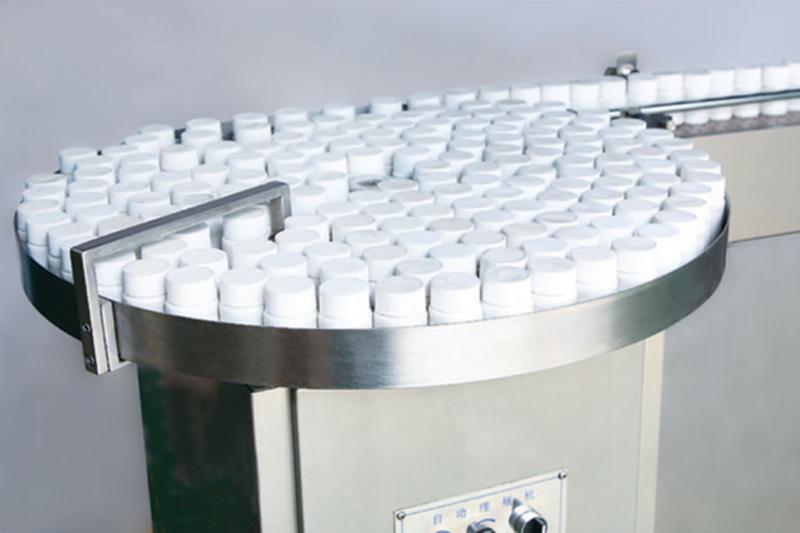
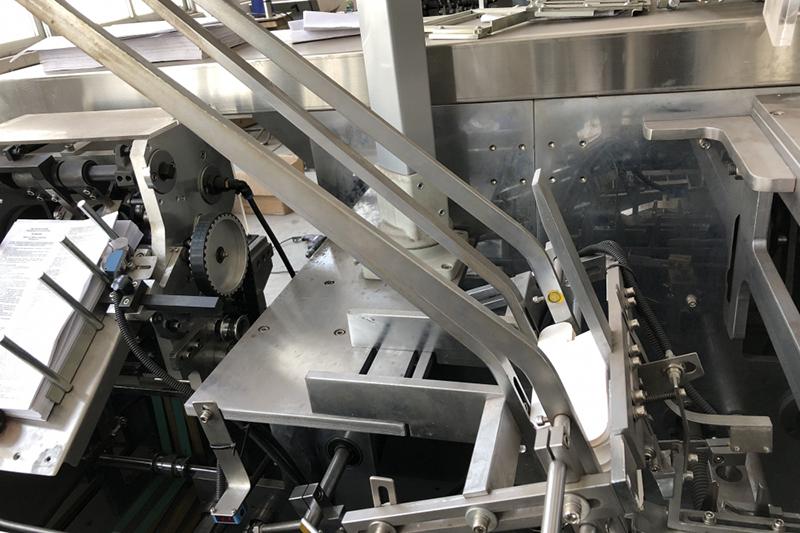
Automatic Horizontal Cartooning Machine
The side load cartoner is a versatile system designed to accommodate various carton sizes with the added convenience of a quick and easy servo-assisted changeover feature. The machine efficiently receives pharmaceutical bottles through a timing screw infeed. The screw aligns and places the bottles into the article buckets of the Pharma Bottles Horizontal Cartoner Machine. As soon as a bottle is detected, the carton is automatically erected, and the bottle is securely inserted into the carton.
China Leading Carton Packaging Machinery Supplier
Our cartoning machine is powerful and highly efficient, meeting the highest standards while incorporating state-of-the-art simplicity. It is constructed from sus 304 stainless steel with hinged cover panels and safety electrical interlocks, and it also includes the door-open shutdown feature.
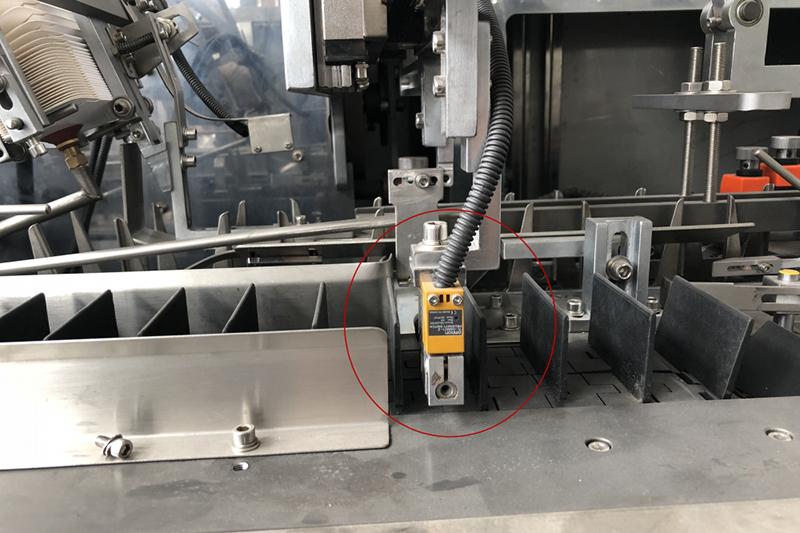
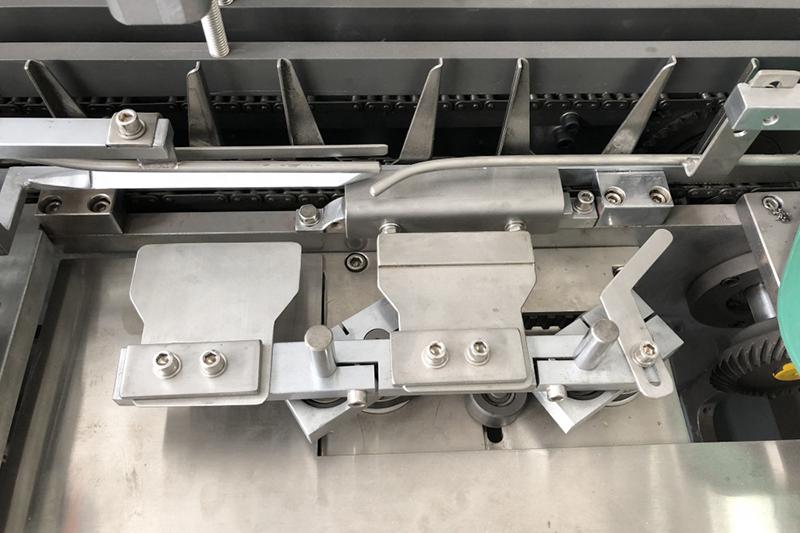
Summary of Cartoning Machine
Our cartoning machines offer a wide range of advantages, including increased efficiency, consistency, versatility, and automation. These benefits lead to improved product quality, reduced labor costs, and enhanced overall productivity, making them essential for modern packaging operations.
Related Products
Machine Features
China Automatic Eye Drop Bottle Cartoning Machine Factory
The eye drop bottle cartoning machine is designed to automatically load bottles into cartons. This versatile machine performs various functions in the packaging process, including bottle unscrambling and feeding, folding and inserting leaflets, forming cartons, inserting bottle and leaflets into the cartons, printing batch numbers, and sealing cartons by either tuck-in or hot melt glue sealing.
They automate various packaging processes, including bottle feeding, leaflet insertion, carton forming, and sealing. This reduces the need for human intervention and minimizes the risk of operator errors.
Bottle cartoning machines are highly efficient and can work at a much faster pace than manual packaging. They can handle a large number of bottles per minute, contributing to increased production rates and reduced labor costs.
Eye drop bottle cartoning machines are designed to accommodate a variety of bottle shapes and sizes, including round and square bottles. This versatility makes them suitable for a wide range of products.
Our eye drop bottle cartoning machines are equipped with quality control mechanisms to detect missing leaflets or bottles. This ensures that only properly packaged products are released, improving overall product quality.
This machines can be seamlessly integrated into existing production lines, connecting with other packaging and filling equipment for a streamlined manufacturing process